|
Jan. 9-19 Jan. 20-23 Jan. 24-27
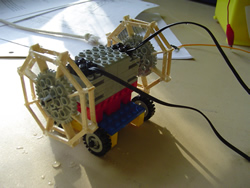
In the end we built all of our waterwheels with hot glue because it
is a lot sturdier than the wood glue (the spokes that were attached
to the 40-tooth gear with wood glue fell off when we touched them).
We also painted the basswood waterwheel with clear nail polish to
make them waterproof. The water wheels may fall apart after sitting
in the water for too long and they have to be robust enough to withstand
multiple trials. This was a very stinky process and drew some strange
looks from professors passing by. While waiting for the waterwheels
to dry (so that we can test them) we worked on other things.
Since we have already fine tuned our first catapult all we have to do is build a second one identical to the first following the instructions at http://www.pienetwork.org/a2z/m/modules/.
Oh no! We just realized that we changed the rubber bands on the original
catapult to a smaller one because we couldn't find a similar size
rubber band for the second catapult. We are going to have to check
to see if the range is still about the same. (Tighter rubber band
(bigger spring constant) = more force!)
We never found any rubber ducks, so we have to build our own floatation
devices to hold the 2 motors. Styrofoam seems like a good floatation
device and it is readily available in the Science Center, so we gave
that a try. We tried various shapes of Styrofoam, but none of them
worked. We even tried embedding the motors into the Styrofoam and
hot gluing the motors on! (Lesson learned . . . hot glue and Styrofoam
is not a good mix because the hot glue melts the Styrofoam and it
gets very stinky!) The problem with the Styrofoam is that the motors
kept flipping over and it is very difficult to find the center of
balance. It may be a better idea to build a car with wheels, but powered
by the waterwheels. This way we don't have to worry about the vehicle
flipping over and drowning the Crickets.
Next we built a small car out of LEGO pieces that was just big enough to hold 2 motors and to keep them dry. The car has 4 small wheels on the bottom.
Before we can get any further, we need to program our remote control
for the waterwheels. While trying to program this remote, we realized
that the crickets read a different resistance values than the HandyBoard
(it must have something to do with the internal resistance of each
of the devices). Basically, the Cricket on the ducks will send out
a different IR signal for each of the buttons (a.k.a. switches) pressed
because they have different resistances. To avoid cross signaling
with our remotes we assigned different IR signals for the two remotes,
even though they have the same configuration (same resistors). We
will eventually build 2 of everything, but for now we only have one
set.
At the moment all the buttons are lined up vertically (forward, left,
right, and backward respectively). To go forward, both motors will
rotate forwards; to go backwards, both motors will reverse directions;
to turn left or right, the motors will operate in opposite directions
(the idea to turn the wheels in opposite directions is credited to
our fellow classmate, Anita Yip . . . more on this later).
The waterwheels work really well. The car can move forwards and backwards
in the water with ease, but it can't turn left or right. We realized
that the car was never going to turn left or right because the car
has 4 wheels and no steering! The car needs to look more like the
SciBorg and have a revolving wheel for the front wheel. Since we don’t
have a small SciBorg wheel, Robbie suggested that we use axle as a
"wheel". What a genius idea! However the car was still unable
to turn. =(
Ah ha! We found our mistake! We made the silly mistake of putting
both of the rear wheels on the same axle. There's no point in having
two motors if one motor is always going to be controlling both wheels!
So we exchanged the back axle for two shorter ones connected by a
connector, now the wheels can move independently of one another. We
originally had only one of the motors on to turn the duck, but the
waterwheel doesn't seem to have enough power to turn the duck. Anita
recommended that we have the waterwheels move in opposite directions!
Yay! Now our duck turns! =)
We demonstrated our remote control ducks to Robbie and Lyn and they suggested that we go back to the floatation idea because it would improve our duck's turning ability due to the fact that that we wouldn't have to worry about friction with the ground. We told Robbie about the problem with finding the center of balance and he informed us that the floatation would work best if the base was a really wide. So our next design will be something similar to an outrigger-canoe, with the Styrofoam extending past our motors. However, for this to work we had to re-design the part that was carrying the motors.
We decided to try out the red motors because they are significantly smaller and less bulky. However, they had less power and it took a really long time for the duck to move. Way too slow, so back to the gray motors. Our ducks work really well with the gray motors.
After 8 hours we finally got the ducks to work as we had envisioned
them to work! The price was the lost of some brain cells due to the
nail polish fumes and the death of one Cricket, but getting the duck
to work was priceless! =) Somehow the cricket aboard the duck got
wet and doesn't work anymore. =( We will have to find a way of keeping
the Cricket dry in the splash zone . . . no more killing Crickets!
(Update: the Cricket didn't really die; itc ame back to life
the next day. We guess it just needs to dry out.)
Wow what a productive day!
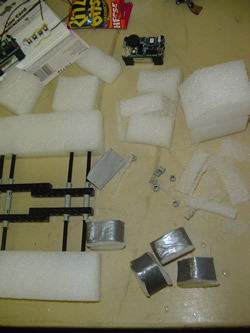
Given the dimensions of our current pool (a under bed storage container:
18 inches by 26 inches) our ducks are going to be way too big. It
is going to be too easy for the ducks to defend their goals. We will
have to make the ducks a lot smaller. First, we shorten the axle that
connects the waterwheel to the motor, and then we also exchanged the
2 big Styrofoam for 4 smaller pieces. This design seems to be pretty
stable.
Now that we have successfully built our first duck we need to build a duplicate. This was very a very time consuming process, but nevertheless tons of fun! =)
The current configuration of our remote is kind of confusing, so we
want to change the position of the buttons, so that it would resemble
a regular remote control. So we have to rewire the whole remote again.
Hmm . . . our remote doesn't seem to work. Oh no! We had our left
and right switches facing the wrong way, so the circuit was open even
without the switches being pressed. Thanks to Robbie for catching
this mistake! After we fixed this mistake, we rewired the remote once
more for aesthetic reasons. =)
Since we changed the rubber bands on our original catapult we had
to retest the range of our catapults. Changing the rubber bands reduced
the firing range of our catapults by half! Yikes! The rubber bands
are not really reliable and we have to find 2 rubber bands of nearly
identical spring constants for them to perform the same. It is amazing
how much difference a rubber band can make. We swapped the pulley
system on the side with an 8-40 tooth gears to reduce the number of
rubber bands involved. Now we are down to one rubber band on each
of the catapult.
We also changed the size of the container holding the ping pong ball on the catapult. Instead of having a paper box, we swapped it for a larger cardboard box. This way it will be more stable and flop around a lot less. The back of the box was also cut out so that it can scoop up the ping pong balls later. We shall figure out the ball re-loading mechanism later and retest the range of the catapult again tomorrow.
The blizzard arrived tonight! Postponement of work... time to go play in the snow!
Wow the blizzard dumped about 2 feet of snow! Time for more sledding down Severance Hill! Back to work on Monday.
|
|
 |